The traditional solution in the steel structure anticorrosion industry is a combination of epoxy zinc-rich primer, epoxy mica intermediate paint and polyurethane topcoat. This traditional solution requires shot blasting or sandblasting surface treatment methods, and rust removal needs to reach Sa2.5 or above. Today, when environmental protection is becoming more and more important, sandblasting, a surface treatment method that causes a lot of noise and dust pollution, is increasingly being questioned.
At the same time, in the traditional anti-corrosion construction process of steel structures, three coats of paint on the bottom, middle and top surfaces are indispensable, which also makes the construction period longer and consumes huge labor costs. Although the price of paint is not expensive, the construction cost often exceeds the cost of paint. The overall painting cost has soared significantly.
If you choose BSC's rust-free polysulfide epoxy coating, these problems will be solved. This product creatively combines adhesive and coating technology, absorbing the strong substrate adhesion characteristics of the adhesive. . This eliminates the need for sandblasting during construction.
As long as loose floating rust is removed, this product can be applied, and the adhesion can reach more than 8MPa. This product has passed the 5000-hour salt spray test and can meet the highest level of anti-corrosion requirements of ISO 12944.
Moreover, the thickness of a single coating of this product can reach more than 250μm, which improves the traditional paint that originally required 4-6 times of application to only 1-2 times of application, greatly speeding up the construction progress and reducing the construction period.
The picture below shows the construction scene of Qiandao Lake Jinzhupai Bridge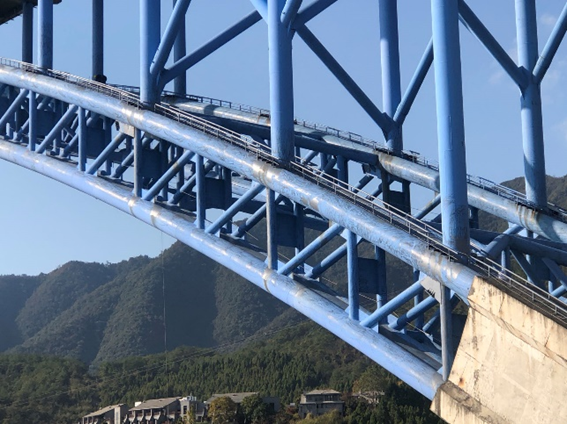
Before construction in 2019, the original paint had peeled off in large areas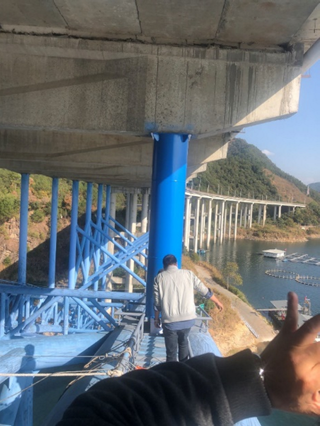
Construction process diagram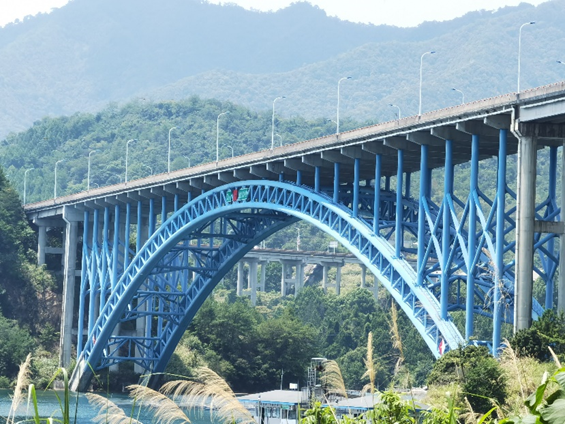
Five years after construction was completed, there was no corrosion or peeling problem